Introduction
Vascular
stents can be used to hold open up arteries that have been occluded by plaque,
which consists of fat, cholesterol, and other molecules. This is usually done by a procedure known as
balloon angioplasty, in which the stent is radially expanded by a balloon at
the specific site so that blood flow can be restored [1]. Because there are many different stents that
have been made, there must be a way to help clinicians to select a particular
stent depending on the type of lesion the patient has. This is important since clinicians want to
improve the condition of the specific patient in the best way possible. However, since there are many kinds of
lesions, performing experimental studies to determine the effectiveness of
different stents becomes very difficult [2]. Also, due to the geometry of the stent, it is
difficult to experimentally determine the stresses and strains as it gets
deformed. As a result, the numerical
approach of the finite element method (FEM) has become very important in the
mechanical analysis of stents [1].
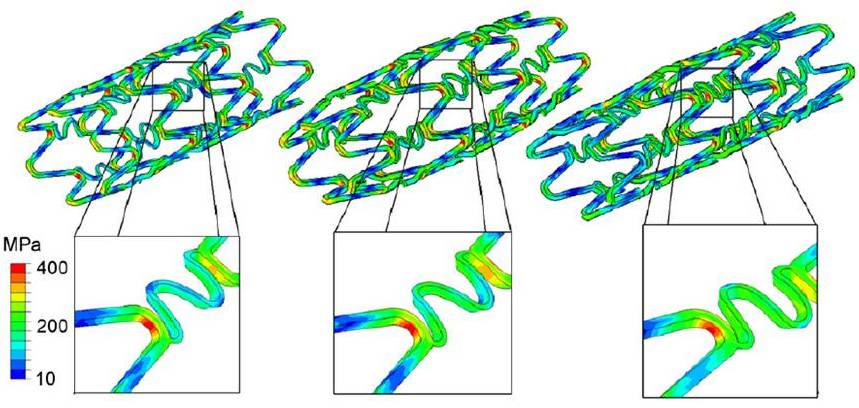
Figure 1. Von mises stresses in Cordis BX-Velocity stent under various loading conditions [3]
In
particular, FEM has become useful in the design of new stents. After a new design is proposed, computer
simulations can be used to evaluate the performance of the stent. This can be done before the creation of a
prototype, thereby saving large sums of money [1]. In this way, the process of optimizing the
design of stents becomes much more efficient.
For instance, FEM has been used to analyze stents as it gets expanded by
balloon angioplasty. Figure 1 shows the
computed von Mises stresses in the Cordis BX-Velocity stent under different
kinds of loadings during balloon angioplasty [3]. Also, it is possible to use FEM to analyze
the mechanical interactions of a stent in an atherosclerotic artery as it gets
deployed [2]. For instance, a 3D model
of a particular nitinol stent design in the blood vessel (common, internal, and
external carotid artery) occluded by plaque is show below in Figure 2 (left). The computed displacements in the arterial
wall and stresses in the arterial wall and stent are shown in Figure 2 (right). Two different stent designs (denoted by “a”
and “b” in Figure 2) were modeled in these simulations [4].
Figure 2.
(left) Meshed model of nitinol stent inside the carotid artery before deployment;
(right) computed displacements (1), first principal stresses
(2),
However,
computational modeling of stents in atherosclerotic arteries is still not an
easy task. The geometry as well as the
material properties of the different components can get quite complicated. Also, there are complex interactions between
the different materials. These physical
interactions include balloon-stent, stent-artery, and balloon-artery, as well
as stent-plaque, and artery-plaque.
Hence, there is still intense research in computational mechanics itself
in order to develop the better algorithms to deal with this [5].
Next >>